Special
トップランナー変圧器、第三次判断基準の適合モデルがデビューへ
第二次から12年、さらなる損失改善で「14.2%」の省エネ効
2025.05.12
トップランナー制度、始まる
1950年代後半に突入した高度経済成長を経て「工業大国」に名を連ねることとなった日本だが、1970年代に発生した2度のオイルショックを背景に、エネルギーの安定供給へと舵を切ることとなった。1979年には「エネルギーの使用の合理化等に関する法律」、いわゆる「省エネ法」が施行され、これを起点にエネルギー消費を改善する動きが始まった(図1)。
そして、省エネが世界的な潮流として確立されるなか、1997年に発表した京都議定書では、1990年を基準に2008~2012年の期間で「平均6%の改善」というエポックメーキングな政策を提案。これを受けて1998年に省エネ法が改正され、機械器具のエネルギー消費効率を改善する「トップランナー制度」が導入された。
特定エネルギー消費機器として11品目から始まったトップランナー制度。2002年には産業機器として変圧器が初めて対象となり(このときは7品目が追加)、第一次判断基準として2006年に油入、2007年にモールドが導入され、トップランナー変圧器の歴史が幕を開けることとなった(図2)。
当初は出荷台数で比較するとモータのほうが多いため、対象機器として議論の的になっていたと想定されるが、変圧器はJEMA(日本電機工業会)で高効率モデルの独自規格をつくっていたこともあり、変圧器が対象になったという経緯がある。政策を実現させる青写真は「可能なものから対象として検討する」というセオリーから考えると、変圧器のほうが改善していく余地があるのかもしれない。
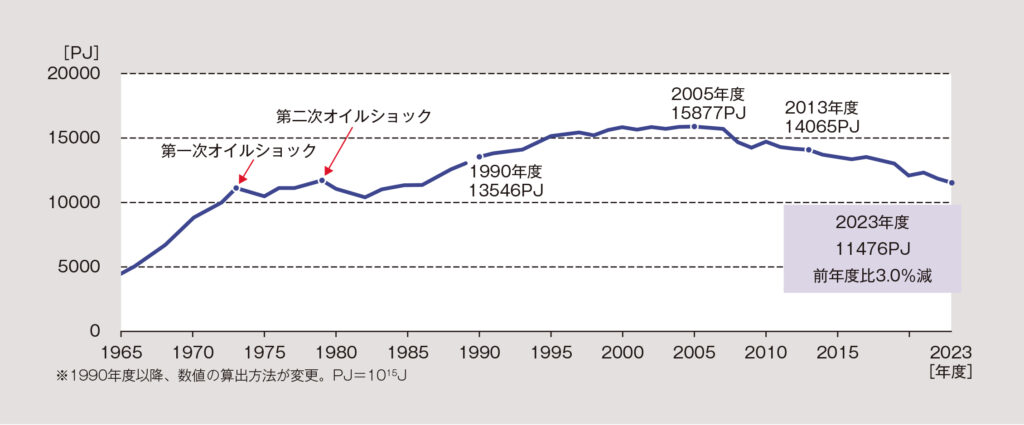
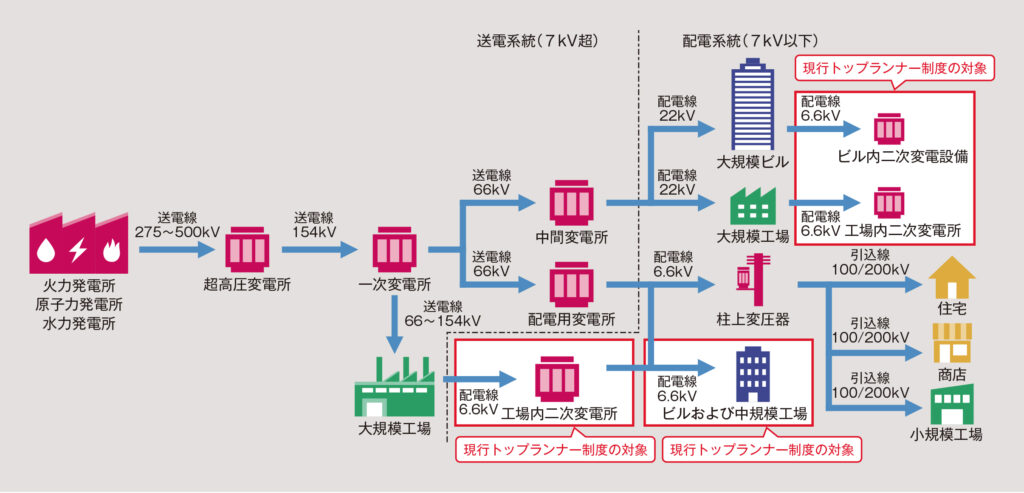
トップランナー変圧器の変遷
ここで、トップランナー制度の対象機器となる3つの要件を整理しておく。
①大量に使用されている機器であること
②使用について、相当量のエネルギーを消費する機器であること
③その機器について、エネルギー消費効率の向上を図ることが特に必要であること
すでに独自規格を導入していたこともあり、トップランナー制度の対象となった変圧器。第一次判断基準として、どれくらい省エネ性能を高めることができるか検討が始まり、油入変圧器に導入された2006年では、1999年に出荷された変圧器と比べて、平均で13.1%の改善が実現したという。
変圧器の場合、エネルギー消費効率の向上には、損失を減らすことが手法として求められる。その損失は「負荷損」と「無負荷損」があり、前者は使用している負荷の割合、つまりは、負荷率によって発生する損失で、後者は常に発生している損失(電化製品の待機電力に相当するもの)を指す。この2つを合わせて全損失となり、トップランナー変圧器として、どれだけ抑えられるかがポイントになってくる。
これらの損失を改善するために、変圧器の構造改革が行われた(図3)。
・負荷損
負荷損は主にコイルで発生する損失で、これを抑えるにはコイルの素材と断面積が関係してくる。素材として電気抵抗やコストの面からアルミや銅が一般的に採用され、導電率の高さから損失低減には「銅」に軍配が上がるが、アルミと比べると単価が高く、比重も大きいので「アルミ」を採用するケースも多い。
一方、断面積を大きくするとコイルの電流密度が小さくなり、損失低減につながる反面、コイルの大型化は避けられない。「銅」と「アルミ」を比較すると、「銅」は導電率が高い分、大型化は抑えられるが、比重が大きいため重くなってしまう。「アルミ」は低コスト&軽量化で有利だが、導電率が低いためコイルの大型化につながる。
変圧器自体の質量とサイズに関係してくることから、組み合わせのバランスを考えて損失を抑える設計が施されているという。
・無負荷損
鉄心で発生する損失が無負荷損で、損失改善には鉄心の「材料」と「構造」が関係してくる。
鉄心といっても、金属の塊を配置しているわけではない。1枚の鋼板を積み重ねていく積層構造を採用し、磁束を通りやすくするために接合部を重ねていく「オーバーステップラップ」で損失改善を実現。さらに、コイルと同様、鉄心の断面積を大きくして磁束密度を小さくする対策も盛り込まれている。
そして「材料」は損失の少ないものを採用する。これが最も効果的な改善だという。
負荷損と無負荷損、この2つの損失低減がメーカー各社のクリアすべき最重要課題となった。
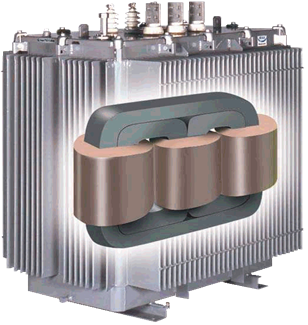
図3 変圧器の鉄心構造。素材はもちろん、コイルの製造方法で損失は大幅に改善する。
空前絶後の大震災が規格に及ぼした影響
独自規格を導入していたこともあり、産業機器として初めて対象となった変圧器。この第一次判断基準で改善した13.1%の省エネ効果を、さらに昇華した規格として2012年に第二次判断基準を発表。2014年度を目標に「トップランナー変圧器2014」が定められた。
この第二次判断基準、2011年に発生した東日本大震災に直面し、付加性能として「耐震」が規格に盛り込まれた。省エネ法とは論点は異なるが、耐震強度の概念を整理し、高めるための手法も提案されたのだ。
「耐震」という要素では、1995年に発生した阪神淡路大震災が1つのターニングポイントとなっていた。変圧器を固定していたボルトが破損し、変圧器がキュービクル内で移動するという被害が多発。これを受けて各メーカーが固定部分を補強していった。
一方、東日本大震災では変圧器の端子と二次側の導体との接続部が破損する被害の報告が大多数を占めたという。これを受けて、耐震機構の設置はもちろん、どのように振動を抑えるか根本的な考え方を検討した。
震災に直面したことで、省エネ効果もブラッシュアップを要求。第一次判断基準と比較して平均18.8%の改善が盛り込まれた。13.1%を実現させた第一次対象モデルから、さらに改善が求められた第二次対象モデル。各メーカーが誇る「技術の粋」が難解なパズルを解き、答えを導き出していったのはいうまでもない。
第一次から第二次へ、省エネ効果を高めるだけでなく、ユーザーにとって使い勝手のいい変圧器とする要求が反映された、ある意味、エポックメーキングと表現できる規格が導入された。
-1024x681.jpg)
-1024x715.jpg)
2026年度を目標に、第三次の開発が急ピッチで進む
2014年から12年、2026年度を導入目標に定められた第三次判断基準の対象モデル、いわゆる「2026トップランナー変圧器」の開発が佳境を迎えている。
第一次、第二次で改善してきた省エネ効果は、第三次で平均11.4%と設定(2019年度の出荷実績と同一条件で比較)。第一次の比較対象である1999年度から、実に45.7%もの改善が見込まれることとなる(図4)。
そもそもの独自規格から、毎回、10%超の省エネ効果を実現しているが、すべての判断基準で改善のポイントは「素材(材質)」と「構造(製造方法)」の2つ。ここで要求性能を満足していくという。第一次からの20年で、省エネ率[%]では45%だが、損失=平均エネルギー消費効率[W]で考えると260W超もの改善が実現している。その大きな要因の1つが「素材」の進化だ。
変圧器の鉄心は、一般には電磁鋼板が主な素材として使用されている。その進化は驚異的で、とりわけ板厚はトップランナー以前と比べて大きく薄板化されているという。
電磁鋼板が薄くなるほど損失が少なくなり、無負荷損の低減につながるだけでなく、負荷損の改善にも有効になる。JEMAの資料では、鉄心素材の1kgあたりの鉄損[W]はトップランナー以前が「1.28」であるのに対し、第二次で「0.83」、第三次では「0.79」が一般的なグレードとして使用されている。
素材自体は電磁鋼板メーカーの技術に頼るしかないが、前述したとおり、鉄心やコイルの構造、それによる質量とサイズのバランスなど、構造は変圧器メーカーが本領を発揮すべき分野。第一次から第二次、第二次から第三次と大きく改善されている。
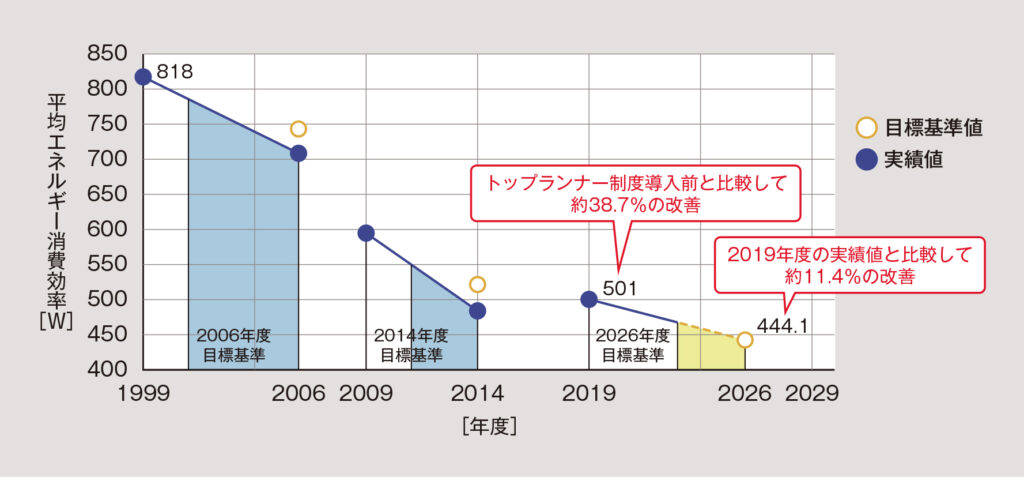
第三次判断基準がもたらした課題
省エネ性能では大きなアドバンテージを得ることができた第三次対象モデル。ユーザーには大きなメリットとなったが、その代償も発生したことが「2026トップランナー変圧器」の特筆すべき点である。変圧器自体がサイズアップすることで、これまで収納されていたキュービクルに設置することが難しくなるという懸念も考えられる。質量も大きくなったため、耐荷重をオーバーしてしまうことに……。
第三次判断基準では、省エネ性能の改善をマストに、どれだけ小型&軽量化を実現させることができるかが大きなポイントになったという。
規定の省エネ性能を盛り込もうとすると、必然的に鉄心を含むコイル部が大きくなってしまう。そうなると変圧器自体もサイズアップせざるを得ない。油入変圧器の場合、本体の面積が冷却性能に関係し、いかに変圧器自体のサイズアップを抑えつつ、冷却面積を広くする構造上の工夫が施されている。そのために独特な「リブ加工」を本体側面に採用しているのだ。
そんな基本構造で、コンパクト化には冷却面積を少なくすることが求められ、つまりは、いかに冷却効率を高められるかがカギを握る。
変圧器は鉄心とコイルが発熱源となり、油入の場合、内部の絶縁油を効率よく自然対流(上部と下部の温度差で絶縁油が対流)させることで冷却効率が高まり、対流がスムーズなほど冷却面積は抑えられる。これにより本体側面の「リブ」の面積が抑えられ、結果、体格としてはコンパクトになるという流れだ。リブ同士の間隔も冷却性能に影響し、狭いと互いが干渉して冷却性能を落としてしまうし、広いとリブ自体の数が少なくなることで冷却面積が小さくなってしまう。この絶妙なバランスがメーカー各社の考え方だという。
「第三次判断基準=サイズアップ」の理由
省エネ性能を最優先させたことで、その実、それぞれの対象モデルで大きくなってはいる。キュービクルに収める場合、ほかの電気機器との離隔距離を厳守するため、例えば、第一次対象モデルから第二次対象モデルに切り替えるときは多少なりとも窮屈ではあった。それをキュービクルに収める電気機器の配置と冷却方法を検討し、課題をクリアしていった。これはキュービクルメーカーの技術がもたらした功績だ。
しかし、第二次対象モデルが現行のキュービクルに収納できた要因の一つに「温度上昇の変更」だという。
第二次判断基準を規定するとき、変圧器の温度の上限が、これまでの「55K」から「65K」に変更された。これにより冷却面積を小さくできるため、変圧器を大きくする必要がないというセオリーが適用できた。省エネ性能の改善に多くの技術を結集できたということだ。
今回のサイズアップは、温度の上限が「65K」を踏襲していることで立ちはだかったハードルであり、ユーザーとしては同じサイズを要求するが、第三次判断基準を満足するとなると不可能に近い。そのために規格を策定する段階からキュービクルメーカーの技術者が参画し、デメリットを最小限に抑えるための協議を重ねていったという。
損失を抑えつつ、いかにコンパクト化&軽量化を盛り込めるか。この二律背反の要素を両立させることが第三次判断基準のキーポイントとなった。
クリアすべき課題がシビアだったためか、2025年1月末の取材時点ではメーカー各社からのニュースリリースが少なく、その動向を詳しくつかめなかった。省エネ性能の改善がもたらす影響、つまりは、第二次対象モデルと比較してサイズも質量も大きくなることについて、おそらく全メーカーが対応に苦慮していたのだろう。検討するハードルは極めて高いことの証明なのかもしれない。
しかし、2026年度のリリースに向けて、着実に歩を進めているのも事実。2025年5月28日から始まる「JECA FAIR 2025」に照準を合わせ、第三次対象モデルの開発が急ピッチで進められているはずだ。目標年度前にPRする最後のビッグステージで、各メーカー、ブラッシュアップを重ねた「2026トップランナー変圧器」を確実に披露してくる。
省エネ性能の改善に対する要求はクリアしてくるとして、サイズと質量への対応について、どのような手を打ってくるか……。ぜひ、注目したいところだ。
第三次判断基準の、その先へ……
2002年から導入されたトップランナー制度を起点に、省エネモードへと突入した変圧器。今回、取材に対応いただいた日立産機システムでは、一般的な電磁鋼板と比べて損失が少なく、より省エネ性能の改善に有効な「アモルファス変圧器」をリリース。さらに、プラスαの要素として「エコ」が求められると、植物由来(大豆)の油を使用した環境調和型モデル「奏」をラインアップに加えている(図5)。
単純に省エネ性能を改善するだけでなく、多様化する時代のニーズを的確にとらえ、迅速に対応した製品開発を信条とし、具現化している。
2025年2月には第7次エネルギー基本計画が閣議決定され、2040年のエネルギー需給見込みとして再生可能エネルギーの割合が初めて50%に達すると発表した。電力需要も大きな伸びが予想され、電源構成も時代を反映して大きく変動しているが、目指すゴールである「2050年、カーボンニュートラル」のビジョンは変わらない。ますます省エネ性能の改善が求められていくだろう。
日本のトップランナー変圧器は2019年で約9万台の出荷が報告されている。この年間出荷台数をベースに、44年後、すべて「2026トップランナー変圧器」に置き換わると、年間で約28.9億kW・hの損失改善につながると試算されている。1台ではわかりにくい効果も、国単位で考えると大きな効果が得られるということだ(図6)。
さまざまな分野で膨大なエネルギーが必要とされている昨今、消費効率を改善するトップランナーの存在は必要不可欠である。変圧器メーカーが解決すべき命題に終わりはない。
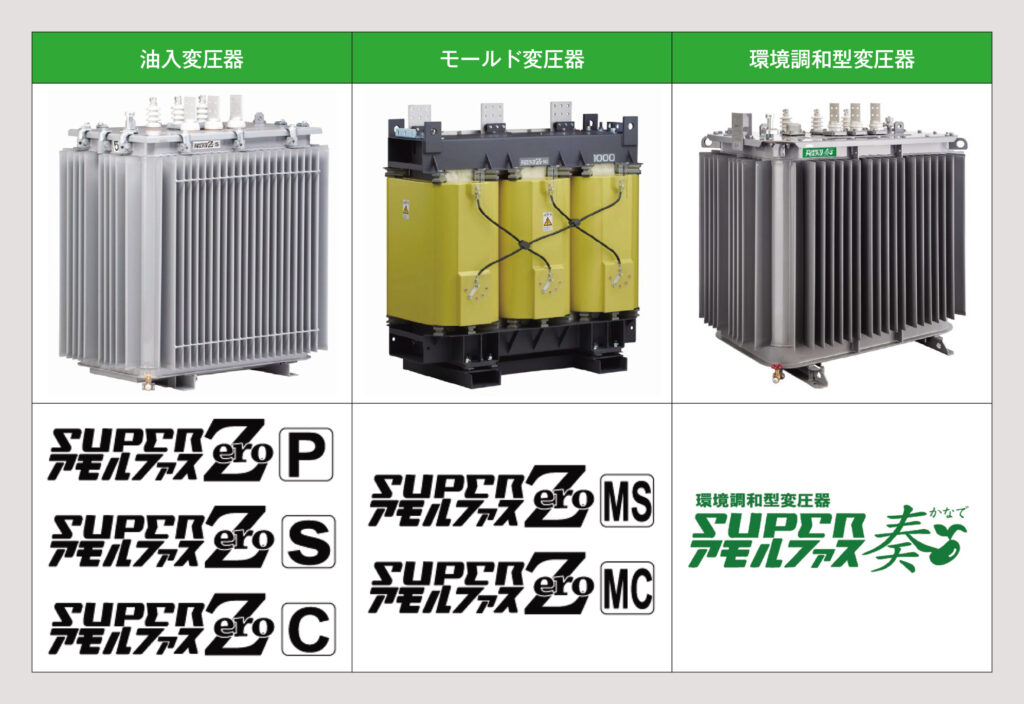
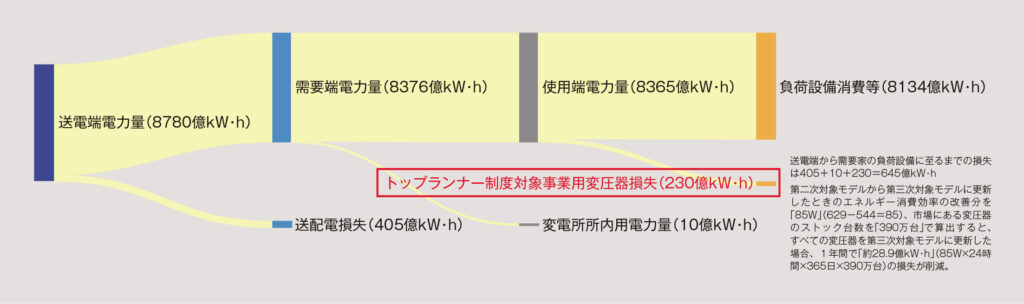
文/編集部、取材協力/株式会社 日立産機システム
関連記事
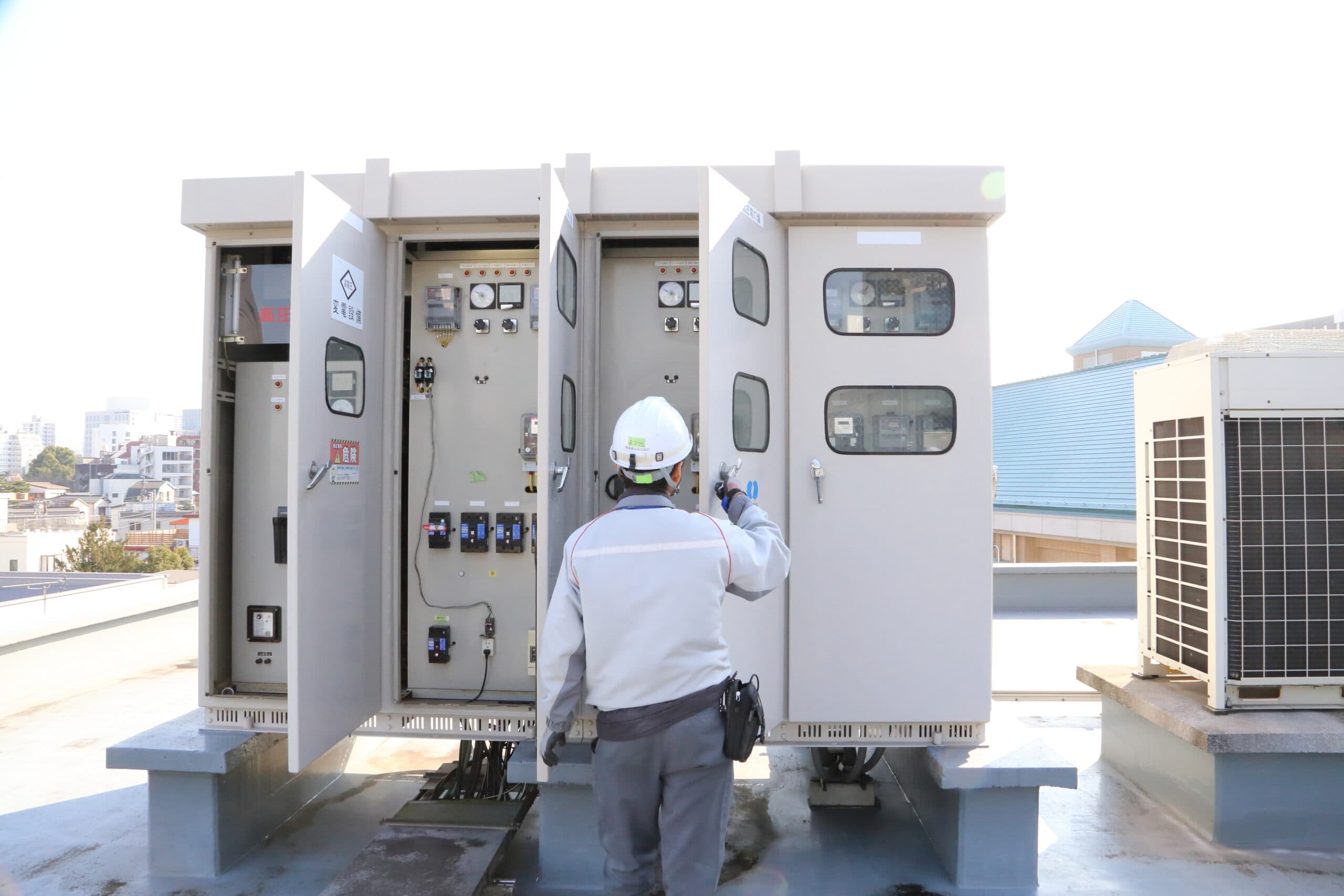
Special

Special

License
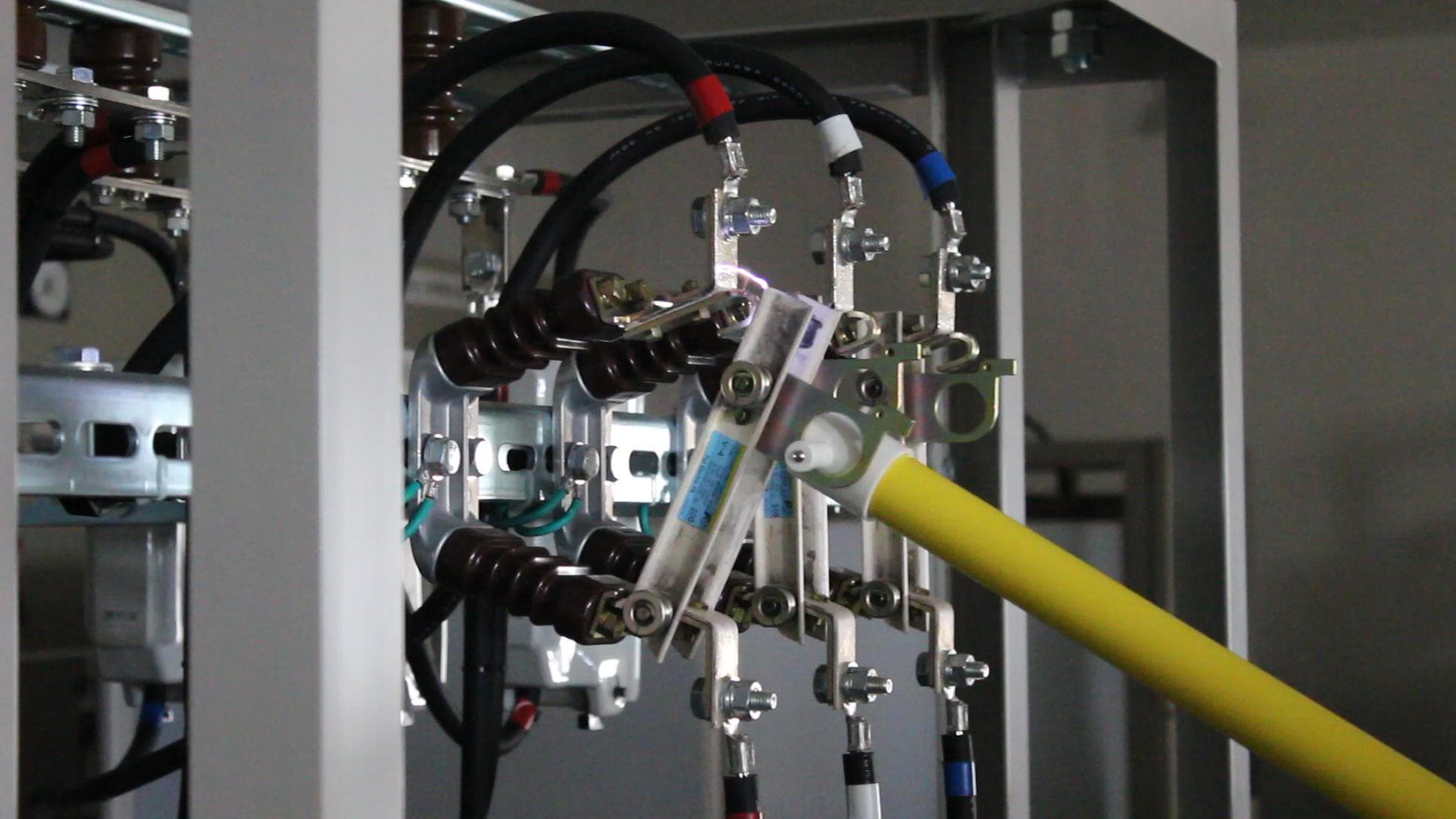
How to

License
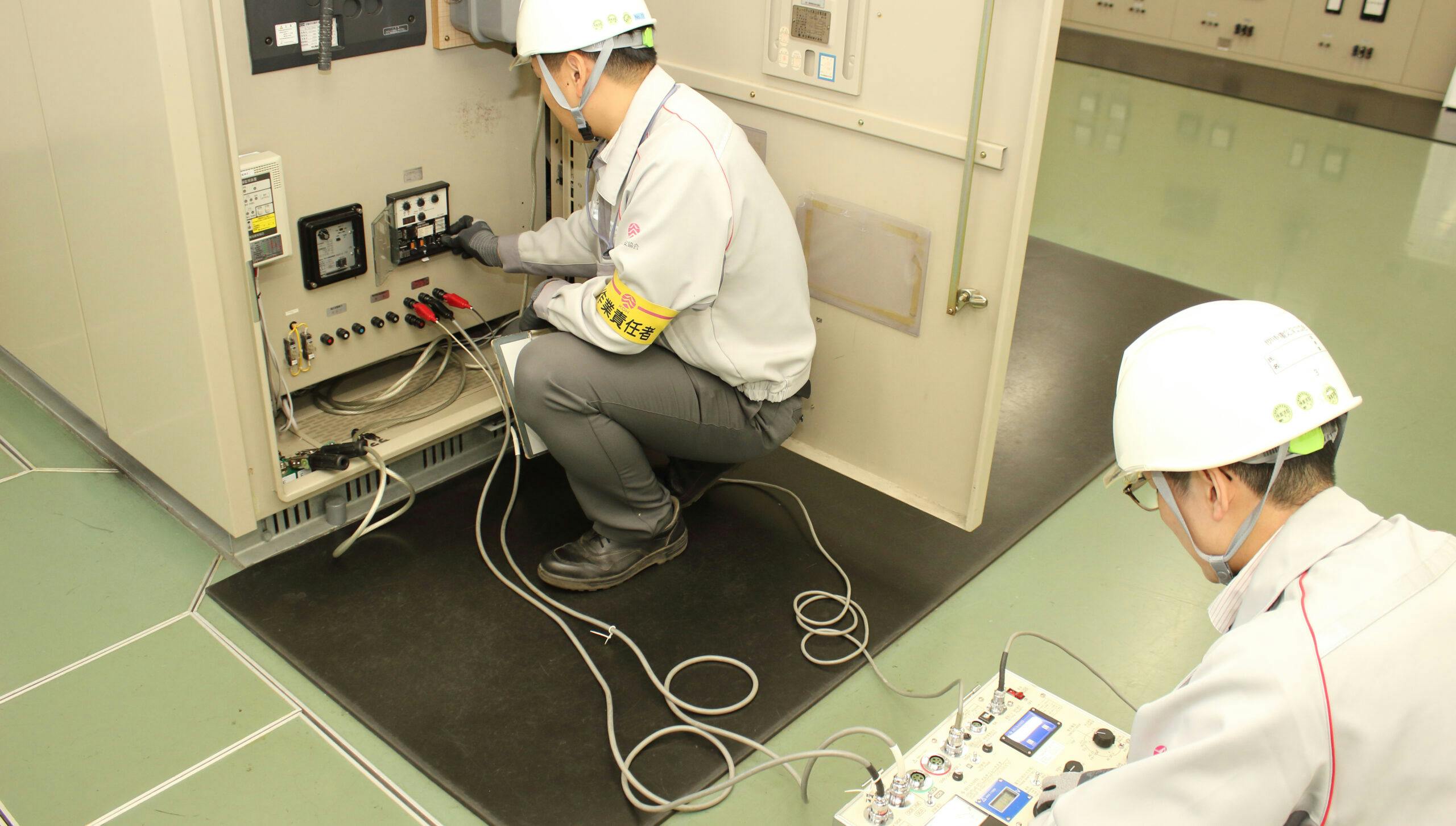
How to
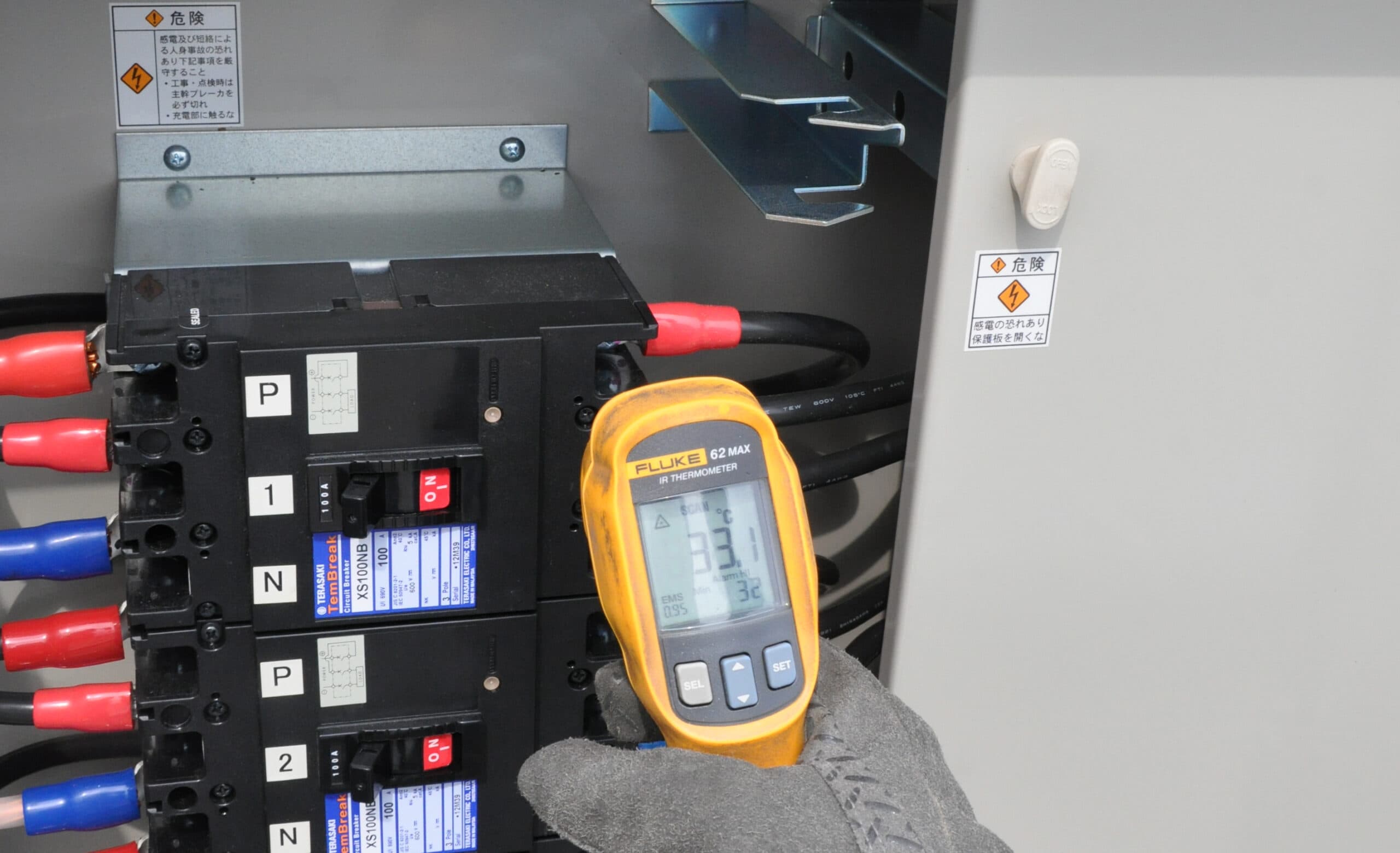
How to
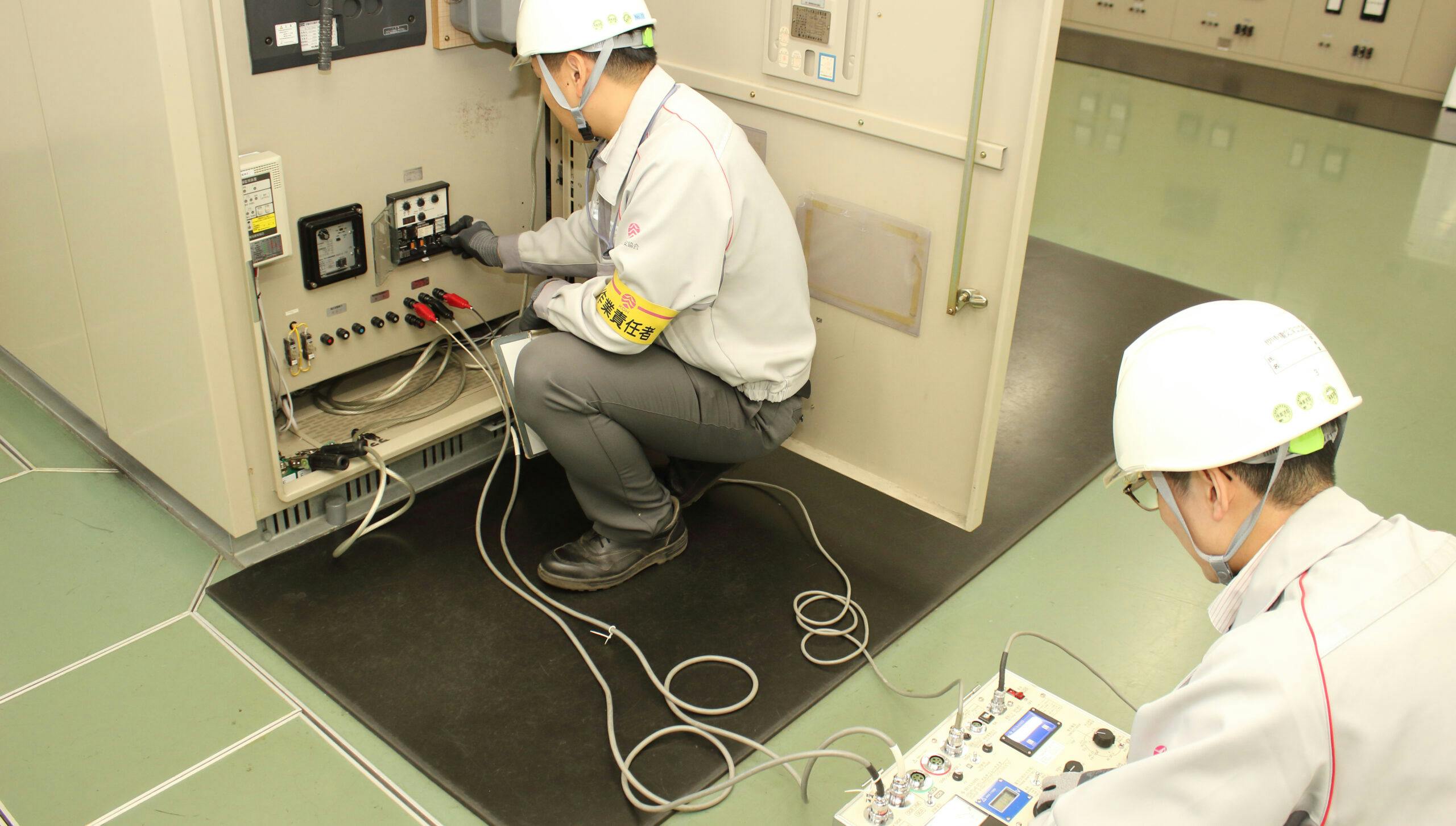
How to